Building a Weblab on Reactors
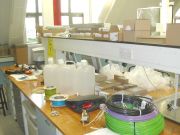
Web Based Teaching
Building a weblab on reactors
In parallel with the sucessful use of the MIT iLabs heat exchanger as part of an exercise, we have been planning for building our own experiment on chemical reactors. Suppliers of custom built experimental equipment were contacted and a collaboration with Siemens Automation was started to use industrial hard and software for control and operation of the experiment and for broadcasting it to the Internet. The result of the efforts described here is the Reactors Weblab.
For the experimental equipment the choice fell on Promech, Sweden, for their experience and ability to design, construct, source necessary parts and manufacture a complete rig to a high standard. During autumn 2005 orders were placed to Promech and Siemens and in the first days of 2006 boxes started to arrive...
The Siemens collaboration enabled us to use industrial hard and software for the control and operation of the experimental rig. The equipment came in hundreds of boxes and the first task was to find out what parts we got and what parts were missing. Luckily, Siemens provided help by sending Dr Simon Baguley. Boxes were opened and parts ticked off against a specification list. The computers were not in the first delivery but the input/output modules could be mounted on racks and installed in the experimental rig to get the wiring up started. The picture shows various boxes with Siemens equipment, cabling and supply tanks for the experimental rig. |
|
|
This picture shows the S7-400 Programmable Logical Controller (PLC), and the four computer screens. In addition to the PLC there are three computers playing four different roles in the Siemens setup; one is the engineering station where the operating system can be programmed and uploaded to the PLC and the graphical interface can be designed and transferred to the operating system server which resides on a second computer. The engineering station doubles as a operating station were the system can be operated via the operating system server. The third computer is the webserver broadcasting a web accessible version of the operating system to the Internet. The experimental rig is visible in the background. |
The experimental rig arrived part assembled but a lot remained to be done. The most time consuming activity was the wiring of all components. All units, apart from the temperature probes, need both a power supply and a connection to a Siemens module. The flow meters and the temperature probes communicate via a fieldbus (profibus PA) whereas the other devices use digital or analogue input/output (I/O) modules. These signals are then communicated to the PLC via a profibus DP cable. Getting the PLC to recognise and being able to read or control the various units also required a lot of time. Here Anders Selmer is wiring up the Siemens Coriolis flowmeters. |
|
|
As soon as the experimental rig was assembled and the piping was completed, we started to perform experiments to test the chemistry. At first we had to control the pumps by separate power supplies borrowed from the electronics workshop but as the devices got connected to the Siemens system, they could be given signals from the engineering station, and once the interface was programmed they could be controlled from the operating station which made life a lot easier. The spectrophotometer proved to be the device that caused the most problems. With advice from Dr Johan Hult in the laser group, the flow cell was modified with a lens which reduced the noice levels. Proper alignment of the fiber optic cables also proved crucial for stability. Teaching Consortium Teaching Fellow Mike Goodson is operating the experiment from the operating station. |
The experimental rig is designed to be flexible and possible to use in a variety of setups. The reactor can be run in batch or continous mode, near ideal to non ideal mode and the volume and temperature can be varied. The chemicals used are 0.2 mol/litre Sodium Hydroxide (NaOH) and 7.2x10-5 mol/litre Phenolphthalein solutions. Phenolphthalein is almost insoluble in water but resonable soluble in alcohol. Hence the Phenolphthalein solution is prepared with 1/8 ethanol. Using less ethanol caused the Phenolphthalein to precipitate despite the low concentration and the results became unpredictable. The progress of the reaction is monitored by measuring the intensity of light at 550 nm going through a flow cell situated at the outlet of the reactor. Anders Selmer adjusting the reactor between two test runs. |
|